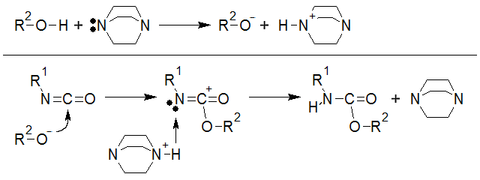
1, Valor de hidroxilo: 1 gramo de polímero de poliol contén hidroxilo (-OH) cantidade equivalente ao número de miligramos de KOH, a unidade mgKOH/g.
2, Equivalente: o peso molecular medio dun grupo funcional.
3, Contido de isocianato: o contido de isocianato na molécula
4, Índice de isocianato: indica o grao de exceso de isocianato na fórmula do poliuretano, normalmente representado pola letra R.
5. Extensor de cadea: Refírese a alcohois e aminas de baixo peso molecular que poden estender, expandir ou formar enlaces cruzados de redes espaciais de cadeas moleculares.
6. Segmento duro: o segmento de cadea formado pola reacción de isocianato, extensor de cadea e reticulante na cadea principal de moléculas de poliuretano, e estes grupos teñen maior enerxía de cohesión, maior volume espacial e maior rixidez.
7, segmento brando: poliol de polímero da cadea principal de carbono de carbono, a flexibilidade é boa, na cadea principal de poliuretano para o segmento da cadea flexible.
8, Método dun paso: refírese ao oligómero poliol, diisocianato, extensor de cadea e catalizador mesturados ao mesmo tempo despois da inxección directa no molde, a unha determinada temperatura do método de moldeo de curado.
9, Método de prepolímero: primeira reacción de prepolimerización de poliol de oligómero e diisocianato, para xerar prepolímero de poliuretano baseado en NCO final, vertido e despois reacción de prepolímero con extensor de cadea, método de preparación de elastómero de poliuretano, chamado método de prepolímero.
10, Método de semiprepolímero: a diferenza entre o método de semiprepolímero e o método de prepolímero é que parte do poliéster poliol ou poliéter poliol engádese ao prepolímero en forma de mestura con extensor de cadea, catalizador, etc.
11, Moldeo por inxección de reacción: Tamén coñecido como Moldeo por inxección de reacción RIM (moldeo por inxección de reacción), mídese mediante oligómeros con baixo peso molecular en forma líquida, mestúranse e inxectan ao mesmo tempo no molde ao mesmo tempo, e a reacción rápida no cavidade do molde, o peso molecular do material aumenta rapidamente. Un proceso para xerar polímeros totalmente novos con novas estruturas de grupo características a velocidades extremadamente altas.
12, Índice de escuma: é dicir, o número de partes de auga utilizadas en 100 partes de poliéter defínese como índice de escuma (IF).
13, Reacción de espuma: xeralmente refírese á reacción de auga e isocianato para producir urea substituída e liberar CO2.
14, Reacción de xel: xeralmente refírese á formación de reacción de carbamato.
15, tempo de xel: baixo certas condicións, o material líquido para formar xel tempo necesario.
16, Tempo lácteo: ao final da zona I, aparece un fenómeno lácteo na mestura de poliuretano en fase líquida. Este tempo chámase tempo de crema na xeración de escuma de poliuretano.
17, Coeficiente de expansión da cadea: refírese á relación entre a cantidade de grupos amino e hidroxilo (unidade: mo1) nos compoñentes do extensor de cadea (incluído o extensor de cadea mixta) coa cantidade de NCO no prepolímero, é dicir, o número molar. (número equivalente) relación do grupo hidróxeno activo a NCO.
18, Poliéter de baixa insaturación: principalmente para o desenvolvemento de PTMG, prezo PPG, insaturación reducida a 0,05 mol/kg, preto do rendemento de PTMG, usando catalizador DMC, a principal variedade de produtos da serie Bayer Acclaim.
19, Disolvente de grao de éster de amoníaco: a produción de disolvente de poliuretano para considerar a forza de disolución, a taxa de volatilización, pero a produción de poliuretano utilizado no disolvente, debe centrarse en ter en conta o NC0 pesado en poliuretano. Non se poden seleccionar disolventes como alcohois e alcohois éter que reaccionan con grupos NCO. O disolvente non pode conter impurezas como auga e alcohol, e non pode conter substancias alcalinas, o que fará que o poliuretano se deteriore.
Non se permite que o éster disolvente conteña auga e non debe conter ácidos e alcohois libres, que reaccionarán cos grupos NCO. O disolvente de éster usado no poliuretano debe ser "disolvente de calidade de éster de amoníaco" de alta pureza. É dicir, o disolvente reacciona co exceso de isocianato e, a continuación, determínase a cantidade de isocianato sen reaccionar con dibutilamina para comprobar se é adecuado para o seu uso. O principio é que o consumo de isocianato non é aplicable, porque mostra que a auga no éster, alcohol e ácido tres consumirá o valor total do isocianato, se se expresa o número de gramos de disolvente necesarios para consumir o grupo leqNCO, o valor é boa estabilidade.
O equivalente de isocianato inferior a 2500 non se usa como disolvente de poliuretano.
A polaridade do disolvente ten unha gran influencia na reacción de formación da resina. Canto maior sexa a polaridade, máis lenta é a reacción, como o tolueno e a metil etil cetona diferenza de 24 veces, a polaridade desta molécula de disolvente é grande, pode formar un enlace de hidróxeno co grupo hidroxilo de alcohol e facer a reacción lenta.
Disolvente de éster policlorado é mellor escoller disolvente aromático, a súa velocidade de reacción é máis rápida que o éster, cetona, como o xileno. O uso de disolventes de éster e cetona pode prolongar a vida útil do poliuretano de dobre ramificación durante a construción. Na produción de revestimentos, a selección do "disolvente de amoníaco" mencionado anteriormente é beneficiosa para os estabilizadores almacenados.
Os disolventes de éster teñen unha forte solubilidade, unha taxa de volatilización moderada, unha baixa toxicidade e úsanse máis, a ciclohexanona tamén se usa máis, os disolventes de hidrocarburos teñen baixa capacidade de disolución de sólidos, menos uso só e máis uso con outros disolventes.
20, Axente de vento físico: axente de vento físico é que os poros da escuma fórmanse a través do cambio da forma física dunha substancia, é dicir, a través da expansión do gas comprimido, a volatilización do líquido ou a disolución do sólido.
21, Axentes espumantes químicos: os axentes espumantes químicos son aqueles que poden liberar gases como dióxido de carbono e nitróxeno despois da descomposición do quecemento e forman poros finos na composición polimérica do composto.
22, Reticulación física: hai algunhas cadeas duras na cadea branda do polímero, e a cadea dura ten as mesmas propiedades físicas que a goma vulcanizada despois da reticulación química a unha temperatura inferior ao punto de reblandecemento ou punto de fusión.
23, Reticulado químico: refírese ao proceso de unir grandes cadeas moleculares a través de enlaces químicos baixo a acción da luz, a calor, a radiación de alta enerxía, a forza mecánica, os ultrasóns e os axentes de reticulación para formar un polímero de estrutura de rede ou forma.
24, índice de escuma: o número de partes de auga equivalente a 100 partes de poliéter defínese como índice de escuma (IF).
25. Que tipos de isocianatos se usan habitualmente en canto á estrutura?
A: alifático: HDI, alicíclico: IPDI,HTDI,HMDI, aromático: TDI,MDI,PAPI,PPDI,NDI.
26. Que tipos de isocianatos se usan habitualmente? Escribe a fórmula estrutural
A: diisocianato de tolueno (TDI), diisocianato de difenilmetano-4,4' (MDI), poliisocianato de polifenilmetano (PAPI), MDI licuado, diisocianato de hexametileno (HDI).
27. Significado de TDI-100 e TDI-80?
R: TDI-100 está composto por diisocianato de tolueno con estrutura 2,4; TDI-80 refírese a unha mestura formada por 80% de diisocianato de tolueno de estrutura 2,4 e 20% de estrutura 2,6.
28. Cales son as características do TDI e do MDI na síntese de materiais de poliuretano?
R: Reactividade para 2,4-TDI e 2,6-TDI. A reactividade do 2,4-TDI é varias veces maior que a do 2,6-TDI, porque o NCO de 4 posicións no 2,4-TDI está moi lonxe do NCO de 2 posicións e do grupo metilo, e hai case ningunha resistencia estérica, mentres que o NCO do 2,6-TDI está afectado polo efecto estérico do grupo ortometilo.
Os dous grupos NCO do MDI están afastados e non hai substituíntes ao redor, polo que a actividade dos dous NCO é relativamente grande. Mesmo se un suboficial participa na reacción, a actividade do suboficial restante diminúe e a actividade aínda é relativamente grande en xeral. Polo tanto, a reactividade do prepolímero de poliuretano MDI é maior que a do prepolímero TDI.
29.HDI, IPDI, MDI, TDI, NDI cal das resistencias ao amarelemento é mellor?
R: HDI (pertence ao diisocianato alifático amarelo invariante), IPDI (feito de resina de poliuretano con boa estabilidade óptica e resistencia química, xeralmente usado para fabricar resina de poliuretano de alta calidade sen decoloración).
30. Finalidade da modificación do MDI e métodos comúns de modificación
R: MDI licuado: propósito modificado: MDI puro licuado é un MDI modificado licuado, que supera algúns defectos do MDI puro (sólido a temperatura ambiente, derretendo cando se usa, o quecemento múltiple afecta o rendemento) e tamén proporciona a base para unha ampla gama. de modificacións para a mellora e mellora do rendemento dos materiais de poliuretano baseados en MDI.
Métodos:
① MDI licuado modificado con uretano.
② MDI licuado modificado con carbodiimida e uretonimina.
31. Que tipos de poliois poliméricos se utilizan habitualmente?
A: poliol de poliéster, poliol de poliéter
32. Cantos métodos de produción industrial hai para poliois de poliéster?
A: Método de fusión ao baleiro B, método de fusión do gas portador C, método de destilación azeotrópica
33. Cales son as estruturas especiais da columna vertebral molecular dos poliois de poliéster e poliéter?
R: Poliéster poliol: un composto de alcohol macromolecular que contén un grupo éster na columna vertebral molecular e un grupo hidroxilo (-OH) no grupo final. Poliois de poliéter: polímeros ou oligómeros que conteñen enlaces éter (-O-) e bandas finais (-Oh) ou grupos amina (-NH2) na estrutura principal da molécula.
34. Cales son os tipos de poliéter poliois segundo as súas características?
R: Poliois de poliéter altamente activos, poliois de poliéter inxertados, poliois de poliéter retardantes de chama, poliois de poliéter modificados heterocíclicos, poliois de politetrahidrofurano.
35. Cantos tipos de poliéteres ordinarios hai segundo o axente de partida?
A: polióxido de propilenglicol, polióxido de propilen triol, poliol de poliéter de burbulla dura, poliol de poliéter de baixa insaturación.
36. Cal é a diferenza entre os poliéteres terminados en hidroxi e os poliéteres terminados en amina?
Os poliéteres aminoterminados son éteres alílicos de polióxido nos que o extremo hidroxilo é substituído por un grupo amina.
37. Que tipos de catalizadores de poliuretano se utilizan habitualmente? Que variedades de uso habitual se inclúen?
R: Os catalizadores de aminas terciarias, as variedades comúnmente usadas son: trietilendiamina, dimetiletanolamina, n-metilmorfolina, N, n-dimetilciclohexamina
Compostos de alquilo metálico, variedades comúnmente utilizadas son: catalizadores de organoestaño, poden ser divididos en octoato estannoso, oleato estannoso, dilaurato de dibutilestaño.
38. Cales son os extendedores ou reticuladores de cadea de poliuretano de uso habitual?
R: Poliois (1, 4-butanodiol), alcohois alicíclicos, alcohois aromáticos, diaminas, aminas alcohólicas (etanolamina, dietanolamina)
39. Mecanismo de reacción dos isocianatos
R: A reacción dos isocianatos con compostos de hidróxeno activo é causada polo centro nucleófilo da molécula de composto de hidróxeno activo que ataca o átomo de carbono baseado en NCO. O mecanismo de reacción é o seguinte:
40. Como afecta a estrutura do isocianato á reactividade dos grupos NCO?
R: A electronegatividade do grupo AR: se o grupo R é un grupo absorbente de electróns, a densidade da nube electrónica do átomo C do grupo -NCO é menor e é máis vulnerable ao ataque dos nucleófilos, é dicir, é máis doado levar a cabo reaccións nucleófilas con alcohois, aminas e outros compostos. Se R é un grupo doador de electróns e transfírese a través da nube electrónica, a densidade da nube electrónica do átomo C do grupo -NCO aumentará, o que o fai menos vulnerable ao ataque dos nucleófilos, e a súa capacidade de reacción con compostos de hidróxeno activos aumentará. diminuír. B. Efecto de indución: debido a que o diisocianato aromático contén dous grupos NCO, cando o primeiro xene -NCO participa na reacción, debido ao efecto conxugado do anel aromático, o grupo -NCO que non participa na reacción desempeñará o papel. do grupo absorbente de electróns, polo que se mellora a actividade de reacción do primeiro grupo NCO, que é o efecto de indución. C. efecto estérico: nas moléculas de diisocianato aromático, se dous grupos -NCO están nun anel aromático ao mesmo tempo, entón a influencia dun grupo NCO na reactividade do outro grupo NCO adoita ser máis significativa. Non obstante, cando dous grupos NCO están situados en aneis aromáticos diferentes na mesma molécula, ou están separados por cadeas hidrocarbonadas ou aneis aromáticos, a interacción entre eles é pequena, e diminúe co aumento da lonxitude da cadea hidrocarburo ou o aumento do número de aneis aromáticos.
41. Tipos de compostos de hidróxeno activo e reactividade NCO
A: NH2 alifático > Grupo aromático Bozui OH > Auga > OH secundario > Fenol OH > Grupo carboxilo > Urea substituída > Amido > Carbamato. (Se a densidade de nubes electrónicas do centro nucleófilo é maior, a electronegatividade é máis forte e a actividade de reacción con isocianato é maior e a velocidade de reacción é máis rápida; se non, a actividade é baixa).
42. Influencia dos compostos hidroxilos na súa reactividade cos isocianatos
R: A reactividade dos compostos de hidróxeno activo (ROH ou RNH2) está relacionada coas propiedades de R, cando R é un grupo atractor de electróns (baixa electronegatividade), é difícil transferir átomos de hidróxeno e a reacción entre compostos de hidróxeno activo e O NCO é máis difícil; Se R é un substituyente doador de electróns, pódese mellorar a reactividade dos compostos de hidróxeno activo con NCO.
43. Para que serve a reacción de isocianato coa auga
R: É unha das reaccións básicas na preparación de escuma de poliuretano. A reacción entre eles produce primeiro un ácido carbámico inestable, que despois se descompón en CO2 e aminas, e se o isocianato está en exceso, a amina resultante reacciona co isocianato para formar unha urea.
44. Na preparación de elastómeros de poliuretano, o contido en auga dos poliois poliméricos debe ser controlado rigorosamente
R: Non se requiren burbullas en elastómeros, revestimentos e fibras, polo que o contido de auga nas materias primas debe controlarse estritamente, normalmente inferior ao 0,05%.
45. Diferenzas nos efectos catalíticos dos catalizadores de amina e estaño nas reaccións de isocianato
R: Os catalizadores de aminas terciarias teñen unha alta eficiencia catalítica para a reacción de isocianato con auga, mentres que os catalizadores de estaño teñen unha alta eficiencia catalítica para a reacción de isocianato con grupo hidroxilo.
46. Por que se pode considerar a resina de poliuretano como un polímero de bloque, e cales son as características da estrutura da cadea?
Resposta: Debido a que o segmento de cadea da resina de poliuretano está composto por segmentos duros e brandos, o segmento duro refírese ao segmento da cadea formado pola reacción de isocianato, extensor de cadea e reticulante na cadea principal de moléculas de poliuretano, e estes grupos teñen maior cohesión. enerxía, maior volume espacial e maior rixidez. O segmento brando refírese ao poliol polimérico da cadea principal de carbono-carbono, que ten unha boa flexibilidade e é un segmento flexible na cadea principal de poliuretano.
47. Cales son os factores que afectan ás propiedades dos materiais de poliuretano?
R: Enerxía de cohesión do grupo, enlace de hidróxeno, cristalinidade, grao de reticulación, peso molecular, segmento duro, segmento brando.
48. Que materias primas son os segmentos brandos e duros da cadea principal de materiais de poliuretano
R: O segmento brando está composto por poliois oligómeros (poliéster, diois de poliéter, etc.), e o segmento duro está composto por poliisocianatos ou a súa combinación con extensores de cadea de moléculas pequenas.
49. Como afectan os segmentos brandos e duros ás propiedades dos materiais de poliuretano?
R: Segmento brando: (1) O peso molecular do segmento brando: supoñendo que o peso molecular do poliuretano é o mesmo, se o segmento brando é poliéster, a resistencia do poliuretano aumentará co aumento do peso molecular de o diol de poliéster; Se o segmento brando é poliéter, a resistencia do poliuretano diminúe co aumento do peso molecular do poliéter diol, pero o alongamento aumenta. (2) A cristalinidade do segmento brando: ten unha maior contribución á cristalinidade do segmento de cadea de poliuretano lineal. En xeral, a cristalización é beneficiosa para mellorar o rendemento dos produtos de poliuretano, pero ás veces a cristalización reduce a flexibilidade do material a baixa temperatura e o polímero cristalino adoita ser opaco.
Segmento duro: o segmento de cadea dura adoita afectar a temperatura de reblandecemento e fusión e as propiedades de alta temperatura do polímero. Os poliuretanos preparados con isocianatos aromáticos conteñen aneis aromáticos ríxidos, polo que a resistencia do polímero no segmento duro aumenta e a resistencia do material é xeralmente maior que a dos poliuretanos de isocianato alifático, pero a resistencia á degradación ultravioleta é pobre e é fácil de amarela. Os poliuretanos alifáticos non amarelen.
50. Clasificación da espuma de poliuretano
R: (1) escuma dura e escuma suave, (2) escuma de alta e baixa densidade, (3) escuma de poliéster, escuma de poliéter, (4) escuma de tipo TDI, escuma de tipo MDI, (5) escuma de poliuretano e escuma de poliisocianurato, (6) método dun paso e produción do método de prepolimerización, método continuo e produción intermitente, (8) escuma de bloque e escuma moldeada.
51. Reaccións básicas na preparación da escuma
R: Refírese á reacción de -NCO con -OH, -NH2 e H2O, e ao reaccionar con poliois, a "reacción do xel" no proceso de espuma refírese xeralmente á reacción de formación de carbamato. Debido a que a materia prima de escuma utiliza materias primas multifuncionais, obtense unha rede entrecruzada, que permite que o sistema de escuma se xere rapidamente.
A reacción de escuma prodúcese no sistema de escuma coa presenza de auga. A chamada "reacción de espuma" refírese xeralmente á reacción de auga e isocianato para producir urea substituída e liberar CO2.
52. Mecanismo de nucleación das burbullas
A materia prima reacciona nun líquido ou depende da temperatura producida pola reacción para producir unha substancia gasosa e volatilizar o gas. Co progreso da reacción e a produción dunha gran cantidade de calor de reacción, a cantidade de substancias gasosas e a volatilización aumentaron continuamente. Cando a concentración de gas aumenta máis alá da concentración de saturación, comeza a formarse unha burbulla sostida na fase de disolución e ascende.
53. O papel do estabilizador de escuma na preparación de escuma de poliuretano
R: Ten o efecto de emulsificación, polo que se mellora a solubilidade mutua entre os compoñentes do material de escuma; Despois da adición de surfactante de silicona, porque reduce moito a tensión superficial γ do líquido, o aumento da enerxía libre necesaria para a dispersión do gas redúcese, polo que é máis probable que o aire disperso na materia prima se nuclee durante o proceso de mestura, o que contribúe á produción de pequenas burbullas e mellora a estabilidade da escuma.
54. Mecanismo de estabilidade da escuma
R: A adición de surfactantes apropiados favorece a formación de dispersión de burbullas finas.
55. Mecanismo de formación de escuma de célula aberta e escuma de célula pechada
R: O mecanismo de formación da escuma de células abertas: na maioría dos casos, cando hai unha gran presión na burbulla, a forza da parede da burbulla formada pola reacción do xel non é alta e a película da parede non pode soportar o estiramento causado. polo aumento da presión do gas, a película da parede da burbulla é tirada e o gas escapa da rotura, formando a escuma de células abertas.
Mecanismo de formación de escuma de células pechadas: para o sistema de burbullas duras, debido á reacción de poliois de poliéter con poliisocianato multifuncional e de baixo peso molecular, a velocidade do xel é relativamente rápida e o gas da burbulla non pode romper a parede da burbulla. , formando así a escuma de células pechadas.
56. Mecanismo de espuma do axente de espuma física e do axente de espuma químico
A: Axente de vento físico: o axente de vento físico é que os poros da escuma fórmanse a través do cambio da forma física dunha determinada substancia, é dicir, a través da expansión do gas comprimido, a volatilización do líquido ou a disolución do sólido.
Axentes espumantes químicos: os axentes espumantes químicos son compostos que, cando se descompoñen pola calor, liberan gases como dióxido de carbono e nitróxeno e forman poros finos na composición do polímero.
57. Método de preparación de escuma de poliuretano branda
R: Método dun paso e método de prepolímero
Método do prepolímero: é dicir, o poliéter poliol e a reacción TDI en exceso convértese nun prepolímero que contén un grupo NCO libre, e despois mestúrase con auga, catalizador, estabilizador, etc., para facer escuma. Método dun paso: unha variedade de materias primas mestúranse directamente no cabezal de mestura mediante o cálculo, e un paso está feito de escuma, que se pode dividir en continuo e intermitente.
58. Características da espumación horizontal e da espumación vertical
Método de placa de presión equilibrada: caracterizado polo uso de papel superior e placa de tapa superior. Método de ranura de desbordamento: caracterizado polo uso de ranura de desbordamento e placa de aterraxe da cinta transportadora.
Características de escuma verticais: pode usar un pequeno fluxo para obter unha gran área de sección transversal de bloques de escuma, e normalmente usa unha máquina de escuma horizontal para obter a mesma sección do bloque, o nivel de fluxo é de 3 a 5 veces maior que o vertical. escuma; Debido á gran sección transversal do bloque de escuma, non hai pel superior nin inferior, e a pel do bordo tamén é fina, polo que a perda de corte redúcese moito. O equipo cobre unha superficie pequena, a altura da planta é duns 12 ~ 13 m e o custo de investimento da planta e do equipo é inferior ao do proceso de espuma horizontal; É doado substituír a tolva e o modelo para producir corpos de escuma cilíndricos ou rectangulares, especialmente tochos de escuma redondos para corte rotativo.
59. Puntos básicos da selección de materias primas para a preparación de espuma suave
R: Poliol: poliol de poliéter para escuma de bloque común, o peso molecular é xeralmente de 3000 ~ 4000, principalmente triol de poliéter. O triol de poliéter cun peso molecular de 4500 ~ 6000 úsase para a escuma de alta resistencia. Co aumento do peso molecular, aumenta a resistencia á tracción, o alongamento e a elasticidade da escuma. A reactividade de poliéteres similares diminuíu. Co aumento do grao funcional do poliéter, a reacción é relativamente acelerada, o grao de reticulación do poliuretano aumenta, a dureza da escuma aumenta e o alongamento diminúe. Isocianato: a materia prima de isocianato da escuma de bloque brando de poliuretano é principalmente diisocianato de tolueno (TDI-80). A actividade relativamente baixa do TDI-65 só se usa para escuma de poliuretano de poliéster ou escuma de poliéter especial. Catalizador: os beneficios catalíticos da espuma suave a granel pódense dividir aproximadamente en dúas categorías: unha é compostos organometálicos, o caprilato estannoso é o máis utilizado; Outro tipo son as aminas terciarias, utilizadas habitualmente como éteres dimetilaminoetílicos. Estabilizador de escuma: na escuma a granel de poliéster de poliuretano utilízanse principalmente surfactantes sen silicio, e na escuma a granel de poliéter utilízase principalmente o copolímero de olefina oxidada con organosílice. Axente de espuma: en xeral, só se usa auga como axente de espuma cando a densidade das burbullas de bloque brando de poliuretano é superior a 21 kg por metro cúbico; Os compostos de baixo punto de ebulición como o cloruro de metileno (MC) úsanse como axentes espumantes auxiliares só en formulacións de baixa densidade.
60. Influencia das condicións ambientais nas propiedades físicas das espumas de bloque
R: O efecto da temperatura: a reacción de espuma do poliuretano acelera a medida que aumenta a temperatura do material, o que provocará o risco de queima do núcleo e lume en formulacións sensibles. A influencia da humidade do aire: co aumento da humidade, debido á reacción do grupo isocianato na escuma coa auga no aire, a dureza da escuma diminúe e o alongamento aumenta. A resistencia á tracción da escuma aumenta co aumento do grupo urea. O efecto da presión atmosférica: para a mesma fórmula, cando se espuma a maior altitude, a densidade redúcese significativamente.
61. A principal diferenza entre o sistema de materias primas utilizado para a escuma suave moldeada en frío e a escuma moldeada en quente
R: As materias primas utilizadas no moldeado de curado en frío teñen unha alta reactividade e non hai necesidade de calefacción externa durante o curado, confiando na calor xerada polo sistema, a reacción de curado pódese completar basicamente en pouco tempo e o molde pode ser liberado nuns minutos despois da inxección de materias primas. A reactividade das materias primas da escuma de moldeo de curado en quente é baixa e a mestura de reacción debe ser quentada xunto co molde despois da formación de escuma no molde, e o produto de escuma pódese liberar despois de que estea completamente madurado na canle de cocción.
62. Cales son as características da escuma suave moldeada en frío en comparación coa escuma moldeada en quente
R: ① O proceso de produción non require calor externo, pode aforrar moita calor; ② Alto coeficiente de caída (relación de colapsabilidade), bo rendemento de confort; ③ Alta taxa de rebote; ④ A escuma sen retardador de chama tamén ten certas propiedades retardantes de chama; ⑤ Ciclo de produción curto, pode aforrar molde, aforrar custos.
63. Características e usos da burbulla branda e da burbulla dura respectivamente
R: Características das burbullas brandas: a estrutura celular das burbullas brandas de poliuretano é maioritariamente aberta. Xeralmente, ten baixa densidade, boa recuperación elástica, absorción de son, permeabilidade ao aire, conservación da calor e outras propiedades. Usos: utilízase principalmente para mobles, material de almofada, material de almofada do asento do vehículo, unha variedade de materiais compostos laminados de recheo suave, escuma suave industrial e civil tamén se usa como materiais de filtro, materiais de illamento acústico, materiais a proba de golpes, materiais decorativos, materiais de embalaxe. e materiais de illamento térmico.
Características da escuma ríxida: a escuma de poliuretano ten un peso lixeiro, unha alta resistencia específica e unha boa estabilidade dimensional; O rendemento de illamento térmico da escuma ríxida de poliuretano é superior. Forte forza adhesiva; Bo rendemento de envellecemento, longa vida adiabática; A mestura de reacción ten unha boa fluidez e pode encher a cavidade ou espazo de forma complexa sen problemas. A materia prima da produción de escuma dura de poliuretano ten alta reactividade, pode lograr un curado rápido e pode acadar unha alta eficiencia e produción en masa na fábrica.
Usos: Úsase como material de illamento para frigoríficos, conxeladores, envases refrixerados, almacenamento frigorífico, illamento de oleodutos e conducións de auga quente, illamento de paredes e tellados de edificios, placa sándwich de illamento, etc.
64. Puntos clave do deseño de fórmulas de burbullas duras
A: Poliois: os poliois de poliéter usados para as formulacións de escuma dura son xeralmente poliois de óxido de polipropileno de alto valor hidroxilo (baixo peso molecular); Isocianato: Na actualidade, o isocianato usado para as burbullas duras é principalmente poliisocianato de polimetileno polifenil (coñecido xeralmente como PAPI), é dicir, MDI bruto e MDI polimerizado; Axentes de vento: (1) axente de vento CFC (2) axente de vento HCFC e HFC (3) axente de vento pentano (4) auga; Estabilizador de escuma: o estabilizador de escuma usado para a formulación de escuma ríxida de poliuretano é xeralmente un polímero de bloque de polidimetilsiloxano e polioxolefina. Na actualidade, a maioría dos estabilizadores de escuma son principalmente de tipo Si-C; Catalizador: o catalizador da formulación de burbullas duras é principalmente amina terciaria, e o catalizador de organoestaño pódese usar en ocasións especiais; Outros aditivos: segundo os requisitos e necesidades dos diferentes usos dos produtos de escuma ríxida de poliuretano, pódense engadir á fórmula retardantes de chama, axentes de apertura, inhibidores de fume, axentes anti-envellecemento, axentes antimoho, axentes endurecedores e outros aditivos.
65. Principio de preparación de escuma de moldaxe de pel enteira
R: A escuma de pel integral (ISF), tamén coñecida como escuma de pelado automático (escuma de pelado automático), é unha escuma de plástico que produce a súa propia pel densa no momento da fabricación.
66. Características e usos dos elastómeros microporosos de poliuretano
R: Características: o elastómero de poliuretano é un polímero en bloque, xeralmente composto por un segmento brando de cadea longa flexible de poliol oligómero, diisocianato e un extensor de cadea para formar un segmento duro, un segmento duro e un segmento brando alternado, formando unha unidade estrutural repetitiva. Ademais de conter grupos éster de amoníaco, o poliuretano pode formar enlaces de hidróxeno dentro e entre moléculas, e os segmentos brandos e duros poden formar rexións de microfase e producir separación de microfases.
67. Cales son as principais características de rendemento dos elastómeros de poliuretano
R: Características de rendemento: 1, alta resistencia e elasticidade, pode estar nunha ampla gama de durezas (Shaw A10 ~ Shaw D75) para manter unha alta elasticidade; Xeralmente, a baixa dureza requirida pódese conseguir sen plastificante, polo que non hai ningún problema causado pola migración do plastificante; 2, baixo a mesma dureza, maior capacidade de carga que outros elastómeros; 3, excelente resistencia ao desgaste, a súa resistencia ao desgaste é de 2 a 10 veces a do caucho natural; 4. Excelente aceite e resistencia química; Poliuretano aromático resistente á radiación; Excelente resistencia ao osíxeno e ao ozono; 5, alta resistencia ao impacto, boa resistencia á fatiga e resistencia ao choque, axeitado para aplicacións de flexión de alta frecuencia; 6, a flexibilidade de baixa temperatura é boa; 7, o poliuretano común non se pode usar por riba de 100 ℃, pero o uso de fórmulas especiais pode soportar 140 ℃ de alta temperatura; 8, os custos de moldaxe e procesamento son relativamente baixos.
68. Os elastómeros de poliuretano clasifícanse segundo os poliois, isocianatos, procesos de fabricación, etc.
A: 1. Segundo a materia prima do poliol oligómero, os elastómeros de poliuretano pódense dividir en tipo de poliéster, tipo de poliéter, tipo de poliolefina, tipo de policarbonato, etc. O tipo de poliéter pódese dividir en tipo de politetrahidrofurano e tipo de óxido de polipropileno segundo variedades específicas; 2. Segundo a diferenza de diisocianato, pódese dividir en elastómeros alifáticos e aromáticos e subdividirse en tipo TDI, tipo MDI, tipo IPDI, tipo NDI e outros tipos; Desde o proceso de fabricación, os elastómeros de poliuretano divídense tradicionalmente en tres categorías: tipo de fundición (CPU), termoplasticidade (TPU) e tipo de mestura (MPU).
69. Cales son os factores que afectan ás propiedades dos elastómeros de poliuretano desde a perspectiva da estrutura molecular?
R: Desde o punto de vista da estrutura molecular, o elastómero de poliuretano é un polímero de bloques, xeralmente composto por polioles oligómeros, segmento suave de cadea longa flexible, diisocianato e extensor de cadea para formar un segmento duro, un segmento duro e un segmento brando alternado, formando unha disposición repetitiva. unidade estrutural. Ademais de conter grupos éster de amoníaco, o poliuretano pode formar enlaces de hidróxeno dentro e entre moléculas, e os segmentos brandos e duros poden formar rexións de microfase e producir separación de microfases. Estas características estruturais fan que os elastómeros de poliuretano teñan unha excelente resistencia ao desgaste e dureza, coñecida como "goma resistente ao desgaste".
70. Diferenza de rendemento entre elastómeros tipo poliéster ordinario e politetrahidrofurano éter
R: As moléculas de poliéster conteñen máis grupos de ésteres polares (-COO-), que poden formar enlaces de hidróxeno intramoleculares fortes, polo que o poliuretano de poliéster ten unha alta resistencia, resistencia ao desgaste e resistencia ao aceite.
O elastómero preparado a partir de poliois de poliéter ten unha boa estabilidade á hidrólise, resistencia á intemperie, flexibilidade á baixa temperatura e resistencia ao mofo. Fonte do artigo / Investigación de aprendizaxe de polímeros

Hora de publicación: 17-xan-2024